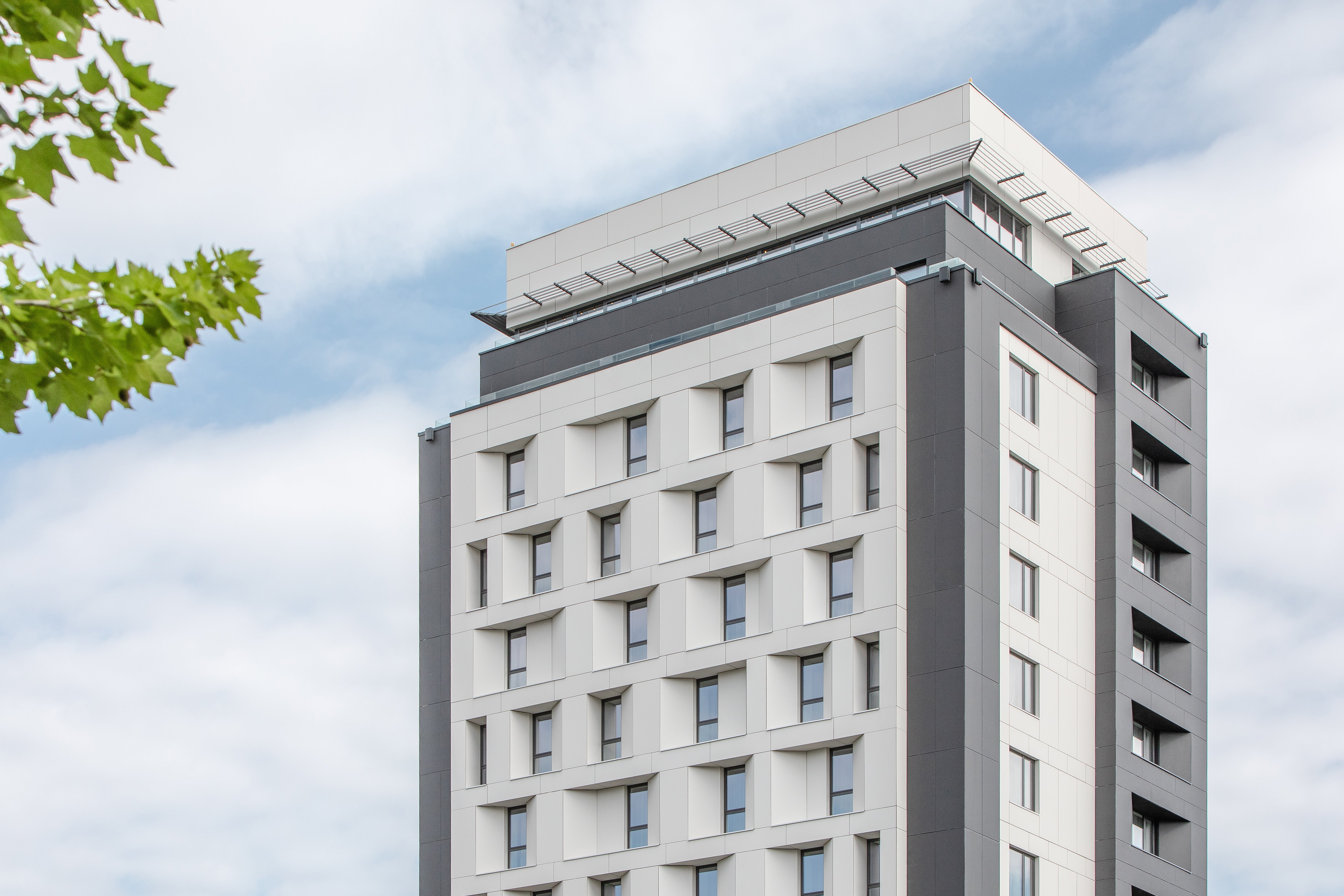
Medium vs. High-Density Fiber Cement
Compare the performance, durability, and design potential of high-density vs. medium-density fiber cement to make the best choice for your project.
Whether you're designing a residential project or a high-performance commercial façade, understanding the difference between high-density (hi-strength) and ordinary medium-density fiber cement is critical. While medium-density options may suffice for basic applications, high-density fiber cement delivers superior performance where it counts—durability, aesthetics, and long-term value.
From resisting moisture and impact to enabling bold, open-joint designs, high-density panels are engineered to meet the demands of modern architecture. In this guide, we’ll break down the key differences to help you choose the right material for your next project.
Medium-density fiber cement typically features a painted, surface-coated finish that can look flat and require trim or sealants that interrupt clean visual lines.
High-density fiber cement offers a crisp, architectural aesthetic with through-colored or factory-finished surfaces and clean edges ideal for modern, open-joint designs.
Grade II
Grade III or Grade IV
Ordinary medium-density fiber cement is typically a drained closed-joint barrier cladding such as in these images showing metal accessories or wood battens around all panels.
Ordinary medium-density fiber cement is often installed with battens or trim pieces that interrupt the clean lines of the design.
High-density fiber cement offers an upgraded aesthetic with open-joint installation for a clean, modern look. Panels can be perforated and routed for enhanced design opportunities.
High-density fiber cement allows for bold, contemporary façades with large-format panels, clean vertical lines, and subtle tonal variation—ideal for modern architectural expression.