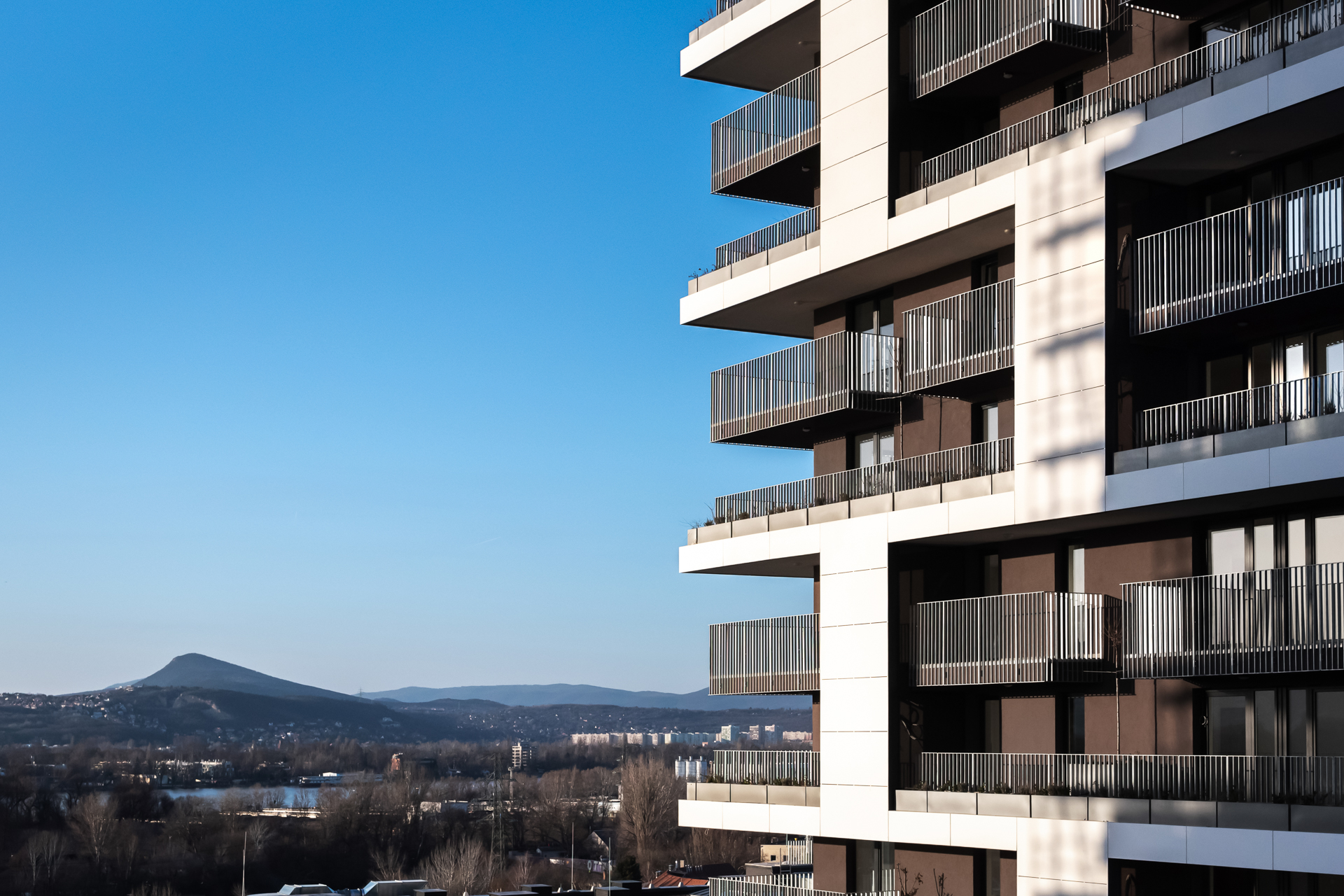
Cut Costs, Not Corners: A Better Façade Alternative
Get premium performance without the premium price. See how high-density fiber cement stacks up against GFRC and UHPC in cost, weight, durability, and design flexibility.
Architects and specifiers sometimes turn to GFRC (Glass Fiber Reinforced Concrete) or UHPC (Ultra-High Performance Concrete) for their strength and aesthetic appeal—but these materials can come with steep costs, long lead times, and complex installation requirements. High-density fiber cement (HDFC) offers a smart alternative, often delivering the look and durability of GFRC or UHPC at a lower total install cost and with easier installation. Ideal for ventilated rainscreen façades, HDFC panels like EQUITONE combine design flexibility, through-colored options, and lightweight performance—all supported by readily available U.S. inventory and on-the-ground manufacturer employee support.
Ultra-High-Performance Concrete (UHPC) emerged in the 1990s to meet specific performance needs in civil and industrial construction. Its distinguishing feature is a denser matrix than standard concrete, achieved through specialized manufacturing and curing techniques.
UHPC is typically produced using a casting process, allowing for a range of shapes, sizes, and textures. As its capabilities became recognized, UHPC found its way into façade construction, where panels often include additional glass fiber mesh within the cement matrix to enhance flexibility.
Glass Fiber Reinforced Concrete (GFRC) shares similarities with UHPC in its use of glass fibers for reinforcement, but it does not achieve the same dense matrix. Developed in the mid-1900s, GFRC incorporates glass fibers directly into the cement mix rather than relying on mesh. This composition allows GFRC to be produced using either casting or spray application methods, enabling flexibility in shaping and forming panels for architectural use.
High-Density Fiber Cement (HDFC) stands out within this category of façade materials due to its unique manufacturing process and performance characteristics. After the initial formation of thin cement and cellulose fiber layers on a forming drum, the material undergoes an extraordinary pressing stage, where 12,000 tons of force compress the panels to create an exceptionally dense, robust product. This process significantly increases durability and strength beyond that of standard fiber cement.
HDFC panels are typically air-cured, but can also be autoclave-cured to achieve even greater consistency, strength, and the potential for unique textures. This combination of density, resilience, and design flexibility positions the material as a premium choice for architects and designers seeking both performance and aesthetic freedom in demanding façade applications.
When GFRC or UHPC becomes cost-prohibitive—or when lead times threaten project timelines—high-density fiber cement offers a proven, high-performance alternative. EQUITONE panels help you maintain your design vision while reducing overall system weight, simplifying installation, and keeping budgets in check. With through-colored options, U.S.-based support, and some readily available inventory, specifying or accepting high-density fiber cement as a substitution is a straightforward, value-driven decision.